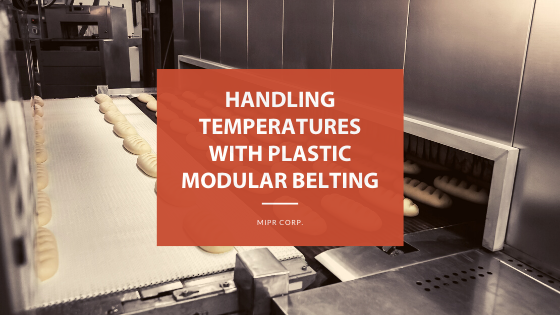
With all the current upheaval and uncertainty in food production and processing, efficiency and safety are top of mind and plastic modular conveyor belts are getting a fresh look from bakeries, meat packers, frozen food distributors, and more. Plastic modular belting has all the advantages of a synthetic belt along with its own unique superpower: the ability to withstand both high heat and freezing cold temperatures and processes in food handling conveyor belt systems. If your production line requires food-grade belting for baking and freezing, see how this FDA-approved conveyor belt can take your business to new places.
Like all synthetic modular belt conveyors, a modular plastic conveyor belt combines lightweight construction with powerful strength, flexibility, and affordability over time. Despite what you may have heard in the past, plastic modular belting now works well on small pulleys and on larger-scale structures, giving it a wider range of potential applications.
Modular Plastic Belting Stays on Track (Even in Complex Configurations)
Plastic conveyor systems run on pure positive drive. Unlike the friction drives needed by other synthetic belts, plastic modular belting utilizes low-tension drive systems. Our own MIPR Corp belting experts find plastic modular conveyor belt designs better preserve proper belt tracking—and good belt tracking is critical to your overall system performance.
Easy to run in tight curves, plastic modular conveyor belts run smoothly and consistently where other belts simply can’t. A plastic modular conveyor belt can go up and down inclines, turn multiple corners, and return to the start using only one motor and one belt. In many cases, plastic conveyor systems let MIPR Corp belting engineers create a single affordable conveyor solution for even for the most complex production lines.
So, where do plastic modular belts sometimes struggle? At very high speeds. As you push a plastic modular plastic belt conveyor faster, you can see a notable increase in noise—a real drawback in some work environments where noise levels need to be kept to a minimum. If you can run steady rather than at high speed, you can run with plastic modular belting.
Modular Plastic Belting is Easy to Clean & Repair
Because plastic conveyor systems are easy to use and install, they are also very easy to clean—and sanitization is another critical component of conveyor belt maintenance, particularly right now. Between changing FDA and USDA requirements and the current outbreak of COVID-19, everyone in food production and distribution is focused on sterilization, cleaning, and maintenance to avoid cross-contamination or infection. (Some types of plastic can react to certain industrial, high strength chemical cleaning agents, so check your plastic modular belting manufacturer standards before implementing a new cleaning or sterilization protocol.)
And should your modular plastic belt ever break down, it will also be easier and faster to repair than many other belting types and styles. Metal mesh belts, for instance, often require complex welding set repairs that lead to longer downtimes, while replacement parts for modular plastic belting systems can simply be snapped into place.
While metal mesh belts used to be the industry standard for food preparation, food-grade modular plastic belting is quickly taking over due to their flexibility, affordability, and ease of use.
Curious about the cost and energy savings that modular plastic conveyor belting can bring to your production line? Talk to the conveyor belt experts at MIPR Corp. We stock and customize a full range of modular plastic belting and we ship samples same-day!